Products Info|failures and analysis of medical sterilization bags
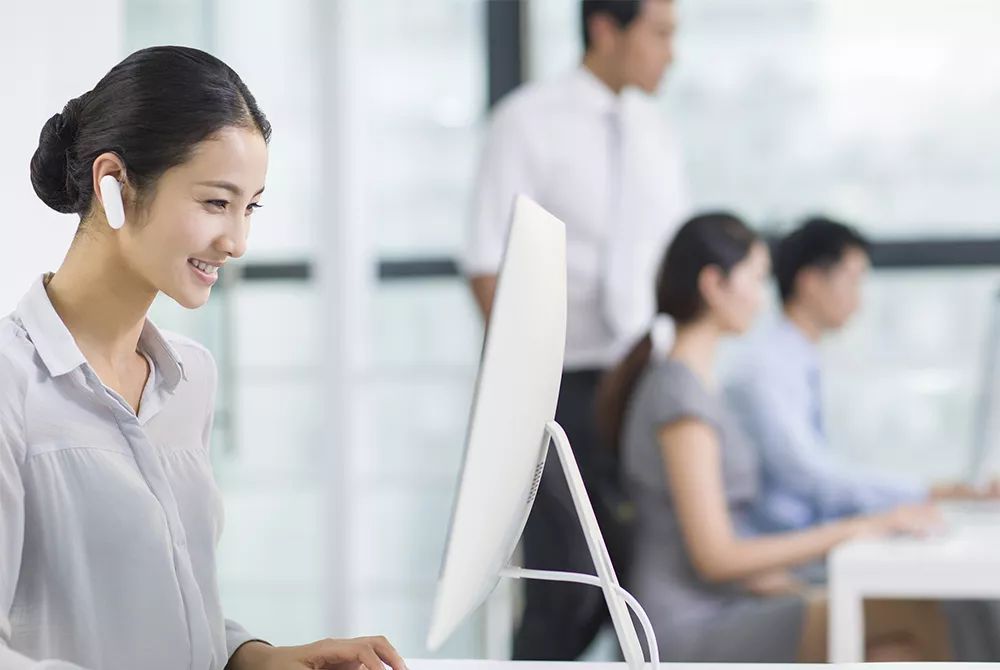
Common failures and analysis of medical sterilization bags
Medical device sterilization bags packaging system, also known as “sterile barrier system”, is an important part of medical devices. It provides packaging and protection for sterile medical devices, which can effectively block microorganisms and bacteria, and can be used within a certain period of time after sterilization. To maintain a sterile environment within the system within the time limit, it is also necessary to meet the sterile presentation and operation of medical devices (such as clean opening).
There are many aspects to consider during the medical device packaging design process: Determine the type of product, will it be sharp, or will it have rough edges? What are the dimensions of the product? What is the sterilization method? etc.
A seemingly intact device package may have safety hazards due to sterile barrier failure.
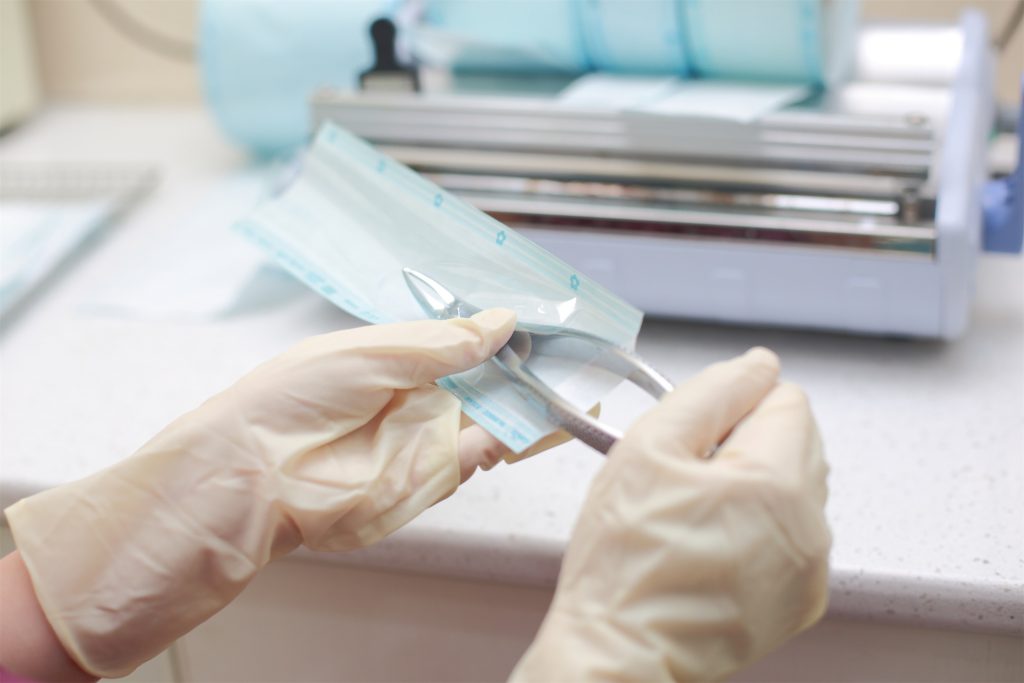
Seal creep
possible reason:
The equipment and packaging are closely matched, and the edges are sealed to bear pressure;
Environmental pressure changes, as well as less breathable materials, experience vacuum and high temperatures (ethylene oxide sterilization).
Countermeasures:
Specially designed glue formula to reduce the risk of sealing creep (water-based glue coating);
Improve the air permeability of top material/cover material (hot melt adhesive coating);
Avoid labels covering breathable windows and optimize boxing layout.
02
Packaging perforation
possible reason:
sharp edges of instruments;
The device and packaging are too tightly matched;
Stress effects between device and membrane;
External puncture.
Countermeasures:
Adjust the bag size;
Use a film with higher puncture resistance.
03
Pleats/sealing channels
possible reason:
The bag is uneven when closed;
Not kept flat during the heat sealing process;
The heat sealing equipment was defective and contaminated.
Countermeasures:
Keep the bag flat during the heat sealing process;
Increase the length of the bag to flatten the heat sealing area;
Check the heat sealing equipment and replace it with qualified heat sealing equipment if necessary;
When sealing, keep the sealing surface clean.
04
Bending and cracking
possible reason:
During transportation, the film bends repeatedly.
Countermeasures:
Adjust package size for better assembly;
Change bag materials (thicker doesn’t always mean better).
05
abrasion
possible reason:
The film forms a “protrusion” and is repeatedly rubbed against the carton.
Countermeasures:
Optimize the design of sterile barriers to reduce “protrusions”;
Design protective packaging to reduce chafing (such as HDPE support cards).
06
Tyvek “rises”
possible reason:
Instruments and bags that don’t fit well can create bruise points, and folding the bag can cause the Tyvek material to delaminate.
Countermeasures:
Adjust the size of the bag for a better fit;
Make sure the Tyvek is not severely bent;
Avoid severe folds and creases.
07
tear delamination
possible reason:
The temperature of the sealing equipment is too high, causing the packaging to be over-sealed;
The packaging material is non-glued;
The packaging design is unreasonable.
Countermeasures:
Packaging using rubberized materials;
Control the temperature, time and pressure of heat sealing;
Reasonably design packaging based on material properties.
08
Penetration or leakage at the seal of the composite aluminum foil bag
possible reason:
The bag is uneven during sealing, the sealing edge width is insufficient, and the pressure or temperature of the sealing equipment is unstable.
Countermeasures:
The seal should be of sufficient width;
Use good packaging machinery, control the heat sealing temperature, time, and pressure. At the same time, the thickness of the heat sealing layer and the thickness of the packaging material must also be appropriate;
Adjust the form of the packaging bag. The three-edge sealed bag has a smaller chance of leakage than other forms (three-dimensional bag).